Vertical Drops
No two geothermal loop systems are the same. The loop system is a series of pipes buried beneath the ground vertically or horizontally, utilizing the constant temperature of the earth to capture thermal energy to heat and cool structures, everything from homes to businesses to public facilities. Installing the pipe loop system requires a unique set of tools, depending on the project site specifics — ground conditions, space constraints, structure size and price.
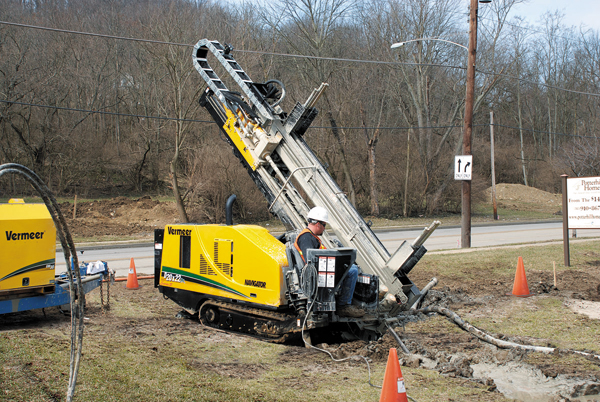
“Each drill site is different, especially with residential geothermal, and so pairing the rig with the right tooling to suit your specific ground conditions is vital,” explains Elliott Duck, sales manager with RigKits LLC (a maker of geothermal drill rigs for the installation of vertical loops and ground source heat pumps).
When it comes to installing big commercial geothermal loops, large drilling equipment is utilized, ranging in cost from $375,000 to $800,000. They’re typically tasked with creating 150- to 500-ft vertical or steep diagonal-angle geothermal boreholes, which will be used to install massive pipe systems in the earth. The pipes will send a mix of water and antifreeze into the earth to absorb thermal energy stored in the ground, bringing that energy back to the surface to heat and cool buildings. It’s cheaper than gas or electric and more environmentally friendly.
When it comes to installing residential geothermal loops, smaller and more nimble equipment is needed, especially since most projects will be retrofits. Residential loop systems can be both vertical and horizontal. If you have enough room, a horizontal system can be installed using trenchers, excavators, backhoes and even horizontal directional drills (HDDs). But if space is limited, and for most homes it usually is, vertical loops are a popular choice. Residential vertical loops require drills.
Many types of ultra-compact vertical and flexible angle drills are now being used for residential retrofits. They are small and powerful, cost much less than commercial equipment and ultimately lower the impact of the drilling process without sacrificing drill speeds.
Many factors affect the size, depth and placement of the loops and the size and type of drill used for residential geothermal drilling. An installer may want to drill three deep wells, but if depth is limited by substrate materials or drilling equipment, six shallower wells may be needed to get the same thermal capacity. No two geothermal loops are the same, so finding the right rig is imperative for conquering unique project challenges.
Geothermal Drill Heads
Most vertical geothermal drills are rotary top head drills that use a feed system to push a rotating drill stem into the ground. Drill heads are driven by hydraulic motors that adjust the speed and torque for efficient drilling depending on the type of material being removed. Looser materials use lower torque and lower speeds, while using casing requires higher torque. When drilling through loose or unconsolidated ground conditions, drillers will often use a steel casing to hold the bore hole open while they continue to drill and insert the loops. This requires high torque.
“That being said,” explains Duck, “when installing geothermal loops, many contractors are now inserting PVC casings as these can be run by hand with the right auger setup.”
A vertical geothermal driller must have a combination of tooling and drill bits depending on what the geology is where the drilling will be done. Most states have water well logs that can be obtained and viewed online, informing drillers what formations were encountered at houses next door or around the corner, so they can be prepared with the right drilling technologies to complete the job.
Mud/Air Drilling Technologies
There are two main types of small vertical drilling — air and mud. Most air drilling is used when boring through hard rock formations. Compressed air runs a percussion drill bit hammer into the earth in a technique called down-the-hole (DTH) hammer drilling. The compressed air is circulated down the inside of the drill stem and forces the material out of the hole. Mud drilling is the most common technology for removing looser soils, clays, sand or gravel. This is a wet rotary drilling method that uses the pressure of water pumped down the hole to push the cuttings upward and flush out the hole.
During mud rotary drilling, water can be mixed with Bentonite clay or various polymers to generate drilling mud that thickens the water and coats the walls of the hole, preventing it from collapsing or caving in on the drill rod. It also reduces the drilling torque and lubricates the bit. A mud pump delivers the mud from a mixing tub to the drill pipe, which takes it to the bottom of the hole, where it moves to the outer walls of the hole and comes back up the drill pipe into the pan or pit and is re-circulated.
With either the air or water method, the cuttings, chips or pieces of rock, clay or earth that are removed are brought up to the surface and shoveled to the side. Depending on the house, customer and situation, many times they are entered back into the landscape.
“It is much more cost-effective to use the mud rotary method because you’re not running a large air compressor which consumes a lot more fuel,” says Darren Swolley, sales manager at SIMCO, an Iowa drill rig manufacturer. “Even though you have to pay to pump the mud or water, it doesn’t really consume any more fuel to run the mud pump if it is part of the drill rig. The air compressor takes more horsepower to run.”
Options that Lower Size and Weight
With smaller equipment, it can be possible to enter yards that would otherwise not have been possible. One way manufacturers are making residential geothermal drills ultra-compact is by mounting the drill on a set of rubber tracks. It can be used in confined spaces where you can’t drive large tandem axle trucks (many rigs today are mounted on chassis cab trucks). Rigs with a dedicated track undercarriage can enter backyards by tracking over a lawn when there is no driveway. At 34 in. wide, some compact all-in-one units can fit through standard residential backyard gates.
“Another way manufacturers can reduce a drill rig’s size is by making it modular,” explains Duck, noting that RigKits is the only manufacturer of modular units in the market. “Modular drills can be about 4 ft wide and weigh 5,000 lbs, allowing them to be towed to a jobsite with a trailer. With optional remote controls to maneuver the tracks, these types of units can easily enter a small yard or tight spaces and be positioned separate from support equipment located further away. Some modular drills offer the power unit separated from the rig itself, which can be mounted on a trailer or welded on an axle to tow behind the rig.”
Drill rigs place a certain amount of down force on the ground during drilling, so manufacturers also offer options to minimize rig weight, which can affect a residential yard. Some drills come with shorter mast heights, which reduce the overall weight of a drilling rig and may be required for residential jobsites that have low headroom. Lower weight can also be achieved by using shorter drilling rods. Ten-foot rods are good for drilling beyond 300 ft and save drilling time compared to using 5-ft rods, but may be overkill for a shallower residential job.
Other ways manufacturers reduce the weight of drill rigs for residential use is by producing thinner walled rods. While not suitable for all applications, such as high torque drilling, they are made from the same steel material and are not only lighter, but allow higher flow volumes than thicker walled rods with similar outer dimensions. When using a quick-thread option, these lightweight rods are easier for one person to handle.
On larger residential jobs requiring long, heavy or large diameter rods, onboard pipe racks and hydraulic automatic rod loading systems can carry hundreds of feet of rods to the drill site and store and feed them into the drill, requiring fewer people to manually load rods which may be stored on the ground or in racks nearby. The drilling rods required by each drilling method determines the overall tolerances and weight allowed.
Flex Angle Drills
In addition to compact vertical drills, flexible angle drills are also designed specifically for residential retrofits. Vermeer is a utility construction equipment manufacturer from Iowa that makes flexible angle drills. Vermeer trenchless product specialist Dave Bokhoven says that drillers typically purchase only one type of drill. Vermeer’s compact units offer the ability to install vertical, horizontal and steep angle loops with the same drill, making it a desirable choice. Flex angle drills use hydraulics to tip the drill stem to any angle between 18 and 90 degrees, allowing a driller to install not only a residential geothermal well but the header pit to the house as well, causing less yard disruption and cleanup.
“Flex angle drills [and geothermal drills overall] have grown in popularity in the residential market because of government and state tax breaks that homeowners can receive by installing geothermal systems,” Bokhoven says.
Debbie Sniderman is an engineer, consultant, writer and CEO of VI Ventures LLC. She can be reached at www.vivllc.com.