Trencher Safety
Trencher equipment manufacturers are always striving to improve their machines and utilize advances in technology to improve safety. However, responsibility for proper trencher operation rests largely on the operator. In order to operate equipment properly, the operator must learn and follow the procedures provided by the manufacturer. Today, as it has always been, safety is a personal choice. We make that personal choice every day, even as we drive to work, when we choose whether or not to obey speed limits. Proper operating procedures, like posted speed limits, are put into place to protect the operator and others who may be around, such as co-workers and bystanders. Listed below are seven primary safety topics that operators, supervisors and managers must all address to help promote a safe working environment when it comes to using trenchers. Â
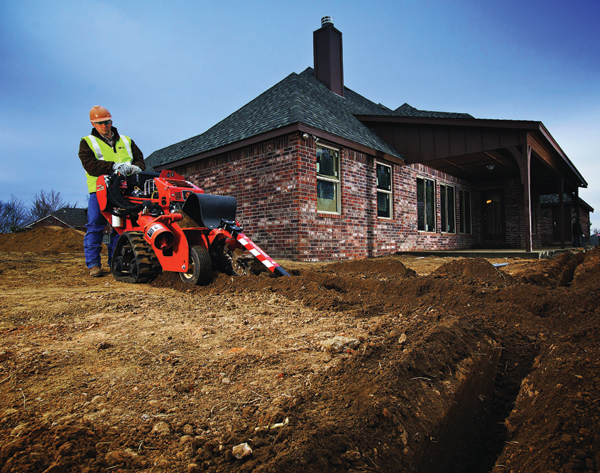
1. Awareness
Thousands of injuries and many deaths occur each year in the construction industry. Many of these can be prevented by being aware of the hazards associated with equipment operation and following the procedures and policies provided by the equipment manufacturer and the employer. Awareness will help an operator and others avoid a hazardous situation that could result in an accident or injury. Employers must be aware of equipment hazards and the manufacturer’s recommended operating procedures in order to develop safe practices and policies. Safe practices do not stop with equipment operation, but also include all aspects of the job.
2. Pre-Work Inspection
Before working with any piece of equipment, several things must take place. First and foremost, the operator needs to read and understand the operator’s manual. The operator should become familiar with the controls and operating procedures. He should only operate the equipment from the designated operator’s position. Next, the operator should also ensure that the trencher is in good operating condition. All guards and shields should be in place. Exposed belts, chains and shafts pose potential hazards. Leaks should be checked with caution.
A good way to determine if a leak is present is to look under the trencher after it has sat overnight. Bare hands should never be used to check for leaks. High pressure fluid escaping from a small hole in a hose or fitting can penetrate skin. Hydraulic poisoning can lead to amputation, or even death, so caution should be exercised. All safety switches must be connected and working according to the manufacturer’s intent. The operator’s manual and the trencher’s safety signs are designed to make operators aware of certain hazards associated with the operation and service of the unit. They should be re-read periodically as a reminder of proper operation. As manuals and safety signs become worn, damaged or misplaced, they should be replaced.
3. Loading and Transporting
When hauling a trencher, the tow vehicle and trailer must be compatible. The tow vehicle must be able to handle the Gross Combined Weight Rating (GCWR) of the tow vehicle and the loaded trailer. Trailer and tow vehicle must be properly connected, and the towing vehicle’s parking brake should be set prior to loading equipment on the trailer. Trailer and tow vehicle should be inspected before and after loading, checking items such as tire condition, working lights, loose items, trailer hookup, etc. Everyone should be clear of the loading area, and the trencher should be in the lowest gear or speed range. It can then be loaded slowly onto the trailer. All attachments not held by stow locks must be lowered, the parking brake set (if supplied) and trencher secured to the trailer with tie-downs. Procedure is reversed for unloading the unit. All state and federal DOT regulations should be observed.
4. Jobsite Preparation
When operating any piece of trenching equipment, worksite hazards must be identified and communicated to everyone on the jobsite. Before beginning any job, the local One-Call service or the national One-Call service at 811 should be contacted to locate and mark all underground utilities. In most cases, this should be done at least 48 hours prior to the start of a job, but local and state regulations for One-Call can vary. Some states may not require all underground utility owners to be members of the One-Call system. In those instances, utility owners must be contacted separately. It is the operator’s responsibility to prevent damage to underground utilities.
The jobsite should be inspected and a visual inventory of the area taken, including looking for signs of buried utilities that may have been missed. These could include trench lines, utility risers or pads, meters, lines coming down utility poles and manholes. Other items that are often overlooked are yard lights, power to outbuildings and underground dog fences. Some of these may be an inconvenience if severed while others can cause serious injury.
5. Potential Hazards
Hazards can vary depending on the jobsite conditions and the equipment being used. When working on slopes, side hills or uneven terrain, a trencher can tip or roll over. Operating on level ground is always preferred if possible. If the trencher is operated from a seated position, the trencher must be equipped with a Rollover Protection System (ROPS), and it must be in place and in good condition. A seatbelt should always be worn with a ROPS in place. Work should be performed with the heaviest part of the trencher facing uphill. When it is necessary to work on a side hill, all attachments should be kept close to the ground and uphill. No one should ever stand on the downhill side of any equipment.
Low-hanging branches or shrubbery can snag control levers or catch on attachments. If it is necessary to operate near trees and shrubbery, care should be taken to keep others away and keep branches lifted out of the way. Operators of trenchers should always be alert and cautious, especially in a crowded area. Bystanders should be kept at least 6 ft away from equipment while in operation.
6. The Danger Zone
Trencher operators must be aware of co-workers and bystanders at all times. Inform co-workers and bystanders to stay at least 6 ft (2 m) from the farthest reach of any attachment including a trencher. Stop operation if anyone enters the danger zone. Bystanders and co-workers within the danger zone may trip and fall into the trench or onto an attachment. The trench could cave-in causing possible entanglement with the attachment. When working in rocky conditions, the trencher can throw rocks from the trench and strike co-workers or bystanders. When operating a machine with an exposed rotating shaft, the danger zone should be extended to 10 ft (3 m). Rotating shafts can entangle clothing and body parts, even if appearing to be smooth material. No one should be allowed near rotating shafts, and no one should ever touch a rotating shaft. Machines should only be operated from the proper designated operator’s position. Fellow workers and bystanders must stay out of the danger zone.
7. Responsibility
Equipment operators are responsible for ensuring a trencher is operated safely and properly. They are responsible for helping to ensure the safety of co-workers and bystanders. However, safety must start with the supervisors and managers requiring that all operators are properly trained on each piece of equipment they operate. Enforcing clearly defined safety policies and procedures and providing the needed training will greatly enhance safety on the job and potentially reduce injuries and fatalities in this industry. Remember, safety is a personal choice that each of us must make. These choices can make a difference on whether we get to go home at the end of each day.
Ricky Harbour is a training specialist for The Charles Machine Works Inc., manufacturer of Ditch Witch products, based in Perry, Okla.