Rehabilitating a Legend
Inside the bowl of iconic Lambeau Field, the eerie silence portended the roar of the crowd like the calm before a storm. Behind the scenes, a new welder generator will help ensure that crowd is bigger in the next year.
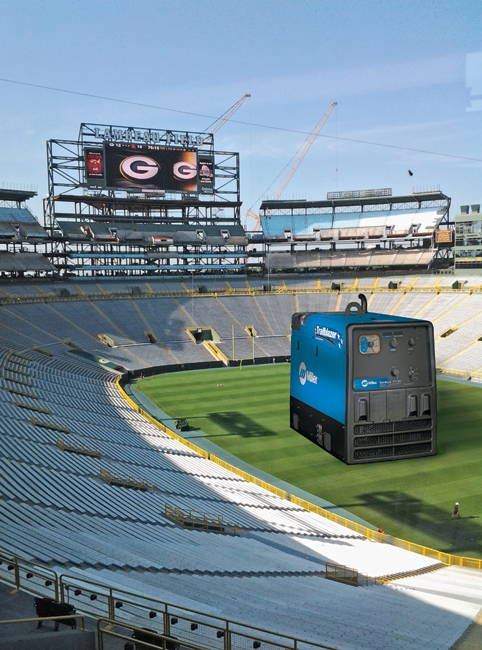
Grounds crew members methodically painted white hash marks onto the pristine green football field. The new scoreboard at the north end zone rotated through displays showing imaginary statistics and a wishful score of 12-10 with Green Bay over Cleveland on the eve of the NFL teams’ preseason match-up that would eventually end in favor of the Browns. That day’s action, however, was focused on the work at the south end zone, where the construction team from Miron Construction Co. Inc. was busily working on a project to expand the stadium.
Based in Neenah, Wis., which is 35 miles southwest of Green Bay, Miron was awarded the contract in September 2011 to update Lambeau Field. The contract called for two jumbo, state-of-the-art scoreboards, the addition of 6,000 new seats, a new entrance at the north side, more elevators and escalators to move fans, a rooftop viewing platform and related structural reinforcements and improvements. The construction at the north side of the stadium is complete, but work will continue through the NFL season on the south end zone renovations.
Throughout the project, Miron has used a menagerie of equipment from Miller Electric, based in nearby Appleton, Wis. Welder generators, air filtration units, preheating devices, safety equipment and a variety of other products have served the crew members as they spruce up the pride of Packers Nation.
The renovation project involved a heavy dose of structural steel work. Miron’s Pete Klosterman, vice president of field services, explained that the work crews had to find a solution to marry the existing structure with the new design. The process required Miron to use plate steel to cap existing columns and provide a base for new columns that were set slightly off center. All told, Klosterman said the project had so far gobbled up more than 4,000 tons of steel.
“A huge push for us was to get the scoreboard in place before the season started,” Klosterman said, adding that the Miron crews erected about 26 tons of steel per day during the height of construction this summer.
Miller invited Compact Equipment and other media outlets to Green Bay to investigate the Lambeau Field jobsite and tour the company’s manufacturing facilities on Aug. 15. As it so happens, the company unveiled a new product for the construction market, and the Miron crew has already put the unit through its paces. Miller hopes its new Trailblazer Series welder generators will change the game by operating more fuel efficiently, more quietly and with a smaller footprint. The Trailblazer 325 and updated 275 build off Miller’s Trailblazer 302. The new models boast up to 50 percent longer run time, using up to 35 percent less fuel, and provide up to 68 percent reduction in sound with an overall smaller footprint (up to 5 in. shorter and up to 108 lbs lighter).
One of the main engineering changes to the Trailblazers involved rotating the engine to the front of the machine, which resulted in a more streamlined airflow and reduced noise. Josh Steiver of Miller’s Power Products Group claimed that 12 of the new Trailblazers make as much noise as one of its preceding models.
The difference between old and new was startling during a product demonstration. The sound contrast was that of a jackhammer vs. a common window AC unit. Welding technicians will appreciate the quieter working atmosphere.
The different engine configuration also involved the addition of a new muffler and a resonator that changes the tonal quality of sound emissions, which makes it a more pleasant sound. I mean, it’s not Mozart, but it won’t rattle your teeth out of your gums either.
The base model Trailblazer comes with standard features such as Smart-Cor and Auto-Speed technology for more efficient power and welding operation and better fuel efficiency, compared to previous models. Options include Excel power outlets to operate a variety of jobsite tools at idle speed, Electronic Fuel Injection (EFI) to improve the air/fuel ratio at all engine speeds, which increases fuel efficiency and engine runtime, and a battery charge/jump start feature that helps reduce fleet downtime.
Miller’s tagline for the new Trailblazer units is “Kicking Gas and Changing the Game.” The company reports that, compared to the prior Trailblazer models, its new welder generators provide annual fuels savings of $462 for the base unit and up to $1,523 for one with all the party favors. The Trailblazer supports welding with stick, wire and TIG modes. With runtimes of 14.5 to 19.5 hours, depending on options, operators can spark and arc all day long. Teamed up with its brethren and at the hands of Miron’s crack construction crew, the new unit will help ensure that Lambeau Field will house Packers fans for years to come.
Brad Kramer is a contributing editor to Compact Equipment, based in Brecksville, Ohio.