Making Safety A Shore Thing
The United States Occupational Safety and Health Administration (OSHA) requires a protective system such as sloping, shielding or shoring for any trench or excavation deeper than 5 ft. Shields and shoring devices protect workers and stabilize the soil around nearby structures or foundations, which can help reduce restoration and cleanup costs. Shoring is the act of supporting walls to prevent a collapse, and it can be passive or active. Trench shields or “trench boxes” passively protect workers within the shield. Shores actively prevent trench walls from collapsing by applying hydraulic pressure to them. Projects for state Departments of Transportation or other government entities typically require active shoring, so nothing in the vicinity of the excavation is compromised. Contractors have many options for purchasing or renting shielding and shoring systems.
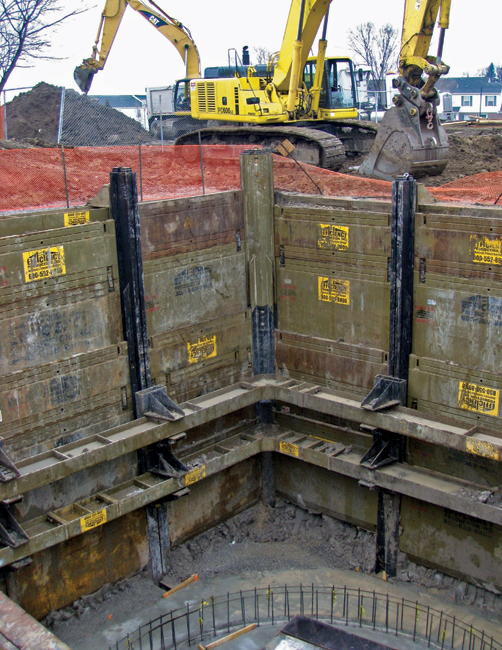
Trench Boxes and Traditional Shields
Conventional trench boxes are a static form of shielding. They are steel side-walled boxes with a cross-member spreader pipe for support. Trench boxes are installed after a hole is dug and before a worker enters.
Manufactured trench shields are rated for a given depth and soil condition and are made from steel or aluminum. James McRay, director of marketing and media at Efficiency Production Inc., says, “Contractors can design protective systems for depths up to 20 ft. If deeper, contractors must use systems designed by a registered professional engineer licensed in the state where work is performed or a manufactured protective system that is in accordance with the manufacturer’s tabulated data. Using a manufactured shield removes the guesswork.”
Manufactured trench shields come with features and options that help when working around utilities already installed in the path of a trench. Cutouts in the shield sidewalls — or specifically designed trench boxes like a manhole shield — accommodate many types of cross utilities.
Efficiency Production, one of the largest manufacturers of trench shoring and shielding equipment, also makes a modular and flexible trench shielding system. Build-a-Box has aluminum panels and corner posts that users can assemble in different configurations. They can stack as many high as needed or form a three- or four-sided box by closing off one or both ends. This system is popular since users can handle and install it with smaller excavation equipment such as a municipal backhoe. Its flexibility works well in cities and other congested areas, making it a popular choice for municipalities, McRay says.
Vertical Hydraulic Shoring Systems
Vertical hydraulic shores also ensure worker safety inside trenches. They consist of a pair of 8-in. aluminum rails connected by hydraulic cylinders. Contractors pressurize the hydraulic cylinders outside of the trench with a hand-pump using environmentally safe shoring fluids composed mainly of water. Hydraulic cylinders are designed to stay pressurized and actively shore a trench for long periods of time, McRay says.
Shoring rails and cylinders come in various lengths. Manufactured hydraulic shores come with tabulated data indicating the number of cylinders required and the spacing of the shores depending on the trench depth and soil conditions. Shores are lightweight and can be easily installed from above. They are typically used in urban settings or in tight places where it’s not feasible to use trench shields or other protective systems. McRay says hydraulic shores work better with harder soil.
Hybrid Manufactured Systems
Manufactured “hybrid” systems mix properties of boxes and shoring. One type is slide rail systems, which consist of steel panels that slide into posts that go in the ground. They are a type of active shoring, and the panels and posts are pushed into the excavation as they are dug. Slide rail systems offer configuration flexibility. They can be used in very large and deep excavations, where shields cannot. At those depths, heavy shields would require a huge excavator for installation, but since slide rail shores are component systems, common-sized excavators can be used.
McRay explains that in large excavations, Efficiency Production’s ClearSpan Slide Rail systems do not require cross-braces for stabilization. Instead, they use free-floating inside waler beams that connect to brackets with rollers to prevent inward deflections. The advantages this offers includes no need for welding steel I-beams onto posts, and therefore no need to cut welds later, and a larger unobstructed working area.
Dan Williamson, national sales manager for Cerda Industries, a trench shoring and shield equipment manufacturer, says while slide rail systems have been around for more than a decade, newer hybrid guide frames have been available for half as long. They are used in pits and very large applications and consist of frames that have steel sheeting in them that can be up to 50 ft wide and 30 ft deep. The sheeting is made from 3/8-in. custom steel with a 5.5-in. profile that slides in a track and can be installed using relatively small machines. Williamson says the technique was modeled after European systems. He says there are 15 systems in Panama and quite a few in the United States.
In addition to slide rails and guide frames, beam-and-plate and large hydraulic brace systems are being used in more expansive and highly-engineered excavations. According to Ron Chilton, president and CEO of National Trench Safety, a national trench shoring and shielding dealer, “These systems use site-specific engineering and will specify the size, materials, structures and equipment to shore the excavation, so it is safe and supports lateral loads and pressures.”
Rental and Purchasing Tips
Chilton says most contractors own a few trench boxes and shores and rent what’s needed for larger projects. “The soil conditions can change in different parts of the job,” he says. “Two blocks down, the soils may be heavier or the job gets deeper, and many contractors don’t want to keep all of the puzzle pieces on hand, like different length spreaders or various box sizes, ready to use.”
For users who perform the same type of work routinely and want to purchase trench boxes or shores, Chilton recommends determining the most common need, so they can be used on future jobs. “Reuse is important, otherwise they become fence guards,” he says.
Next, he says, work with a company that has a wide inventory and the ability to show proper uses and installation techniques. After-the-sale support is also important. He recommends working with a company that provides on-site consultation assistance for future projects to show how the equipment can and cannot be used. Last, he recommends finding a high-quality product that’s built to industry and OSHA standards.
Williamson adds holes can be safely shored in many ways. Not one product will do everything. To determine the right type of product to purchase, first know the capacity of the machine you will use for installation.
Then know the pipe or manhole diameter and excavation depth. Finally, know the soil conditions and infrastructure, such as buildings, curbs or other utilities.
Contractors who are new to shoring can use the expertise of the manufacturer from the pre-bid design and project proposal stage to installation and pulling the pieces out when the project is done.
Debbie Sniderman is a contributing editor to Compact Equipment, based in Charleston, S.C. She can be reached at www.vivllc.com.