Grading Productivity Systems
People attached to slim screen laptops while sipping a cup of coffee. News reports of genetically engineered salmon. A computerized voice giving turn-by-turn directions. There are times when 21st century technology makes you take a step back and marvel at our evolution. In the construction industry, there is perhaps no more impressive technology than the development of global positioning systems (GPS) grading products.
Communicating with satellites orbiting the earth, GPS grading systems coupled to the machines can control the pitch of a dozer’s blade or alert your excavator operator that he’s missing the mark. The systems from the likes of Topcon, Leica Geosystems and Trimble create a three-dimensional (3D) map of the jobsite in the cab of your motorgrader, dozer, excavator, backhoe loader or skid steer.
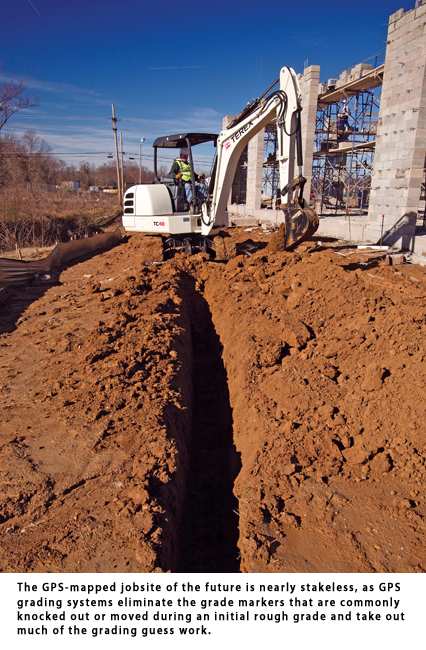
The challenging economy of the past year and a half has pushed contractors to find ways to bid more competitively and to do more with the machines they own today. Today’s business owners are becoming more educated and technology savvy. In the past two years, GPS grading systems have gained acceptance as they’ve reached a new level of accuracy.
“When [Caterpillar] released its first AccuGrade GPS systems, we were only utilizing the U.S. Navstar satellites,” explains John Thomas, Caterpillar Inc.’s Connected Worksite Marketing Consultant. “Then we improved our systems by providing the capability to also utilize the GLONAS satellite network. This provided better satellite coverage and improved accuracies.”
Caterpillar got serious about its AccuGrade GPS systems two years ago when it joined with Trimble, a company that integrates a wide range of positioning technologies, including GPS, laser, optical and inertial technologies, with application software, wireless communications and services to provide complete commercial solutions, to create a new company — Virtual Site Solutions.
While laser systems have been doing grading work for the better part of the past 30 years, GPS is starting to gain mainstream acceptance with contractors because of the technology’s ability to be used throughout the job process. The systems can take a two-dimensional (2D) IOCAD data file (the job blueprints) and turn it into a 3D digital terrain model — giving you a virtual jobsite that you can plan your attack on before setting foot on the jobsite.
After you have the digital model, you have to localize the jobsite. This means that you are taking the jobsite and tying its physical position with that of the satellites’ position. This is done by walking around the jobsite and placing the hand held GPS rover for a short amount of time on control points put in by the surveyor. The number of points depends upon the size and layout of the jobsite, but you need to provide at least four.
You then take the file from the rover unit and put it into the GPS control box on the excavator, grader, loader or dozer. Now, the GPS system knows where the machine is on the jobsite and its activity in the programmed job.
The operator will have access to the data and where he needs to be digging to give him a more complete picture of the job he’s doing. That way he can think beyond just controlling the blade to stay on grade.
Beyond that, the operator can also use GPS grading systems to plan beyond the initial stages of the project. For example, he might pile material up on a jobsite during a rough grade and then find out in the next phase that the material has to move to another spot. By analyzing it with the GPS system first and planning the job ahead of time, the operator can move the material to the proper place the first time.
“It provides a better understanding of the job and the work to be done,” says Thomas. “It’s easier for the operator to get an image in his or her head of what the final grade should look like. When changes to the site plans occur, and they will, those changes can be uploaded into the machine in seconds, instead of waiting for surveyors to re-stake the job.”
The GPS-mapped jobsite of the future is nearly stakeless, as GPS grading systems eliminate the grade
markers that are commonly knocked out or moved during an initial rough grade and take out much of the grading guess work. Keep in mind that it doesn’t eliminate the need to check the grades — you still have to comply with all the regional and local rules and regulations — but it does increase the odds of success that the first pass by the operator is the right pass that puts the grade where it needs to be on the first check, not the third or fourth.
Jumping into GPS technology can be intimidating, but it’s gotten easier with several manufacturers, including Caterpillar, offering factory-integration. Order a dozer and get the AccuGrade system pre-installed, and you’d just need to invest in the other equipment like GPS base station and rover. It’s not a cheap investment. Complete, stand-alone GPS systems run $30,000 to $55,000, not including the $20,000 base station. The trade-off is that once the major investment is made, you can add components such as a laser or sonic system at a fraction of the starting cost.
Right now, a rental purchase option (RPO) is a popular route to GPS system efficiency. Think of it as a
try-before-you-buy option. You get to take the technology for a spin and see how it can improve your bottom line before taking the plunge.
Jason Morgan is a contributing editor to Compact Equipment and an associate editor to sister publication Utility Contractor, both based in Peninsula, Ohio.
Comments are closed here.