Getting Tired
Matching the right tire to your application can help save thousands of dollars down the road. Skid steer owners take note. Selecting the right tires for your skid steer can have a significant effect on the performance of your machine. In addition, selecting tires that don’t provide extended wear characteristics can have a negative effect on your wallet.
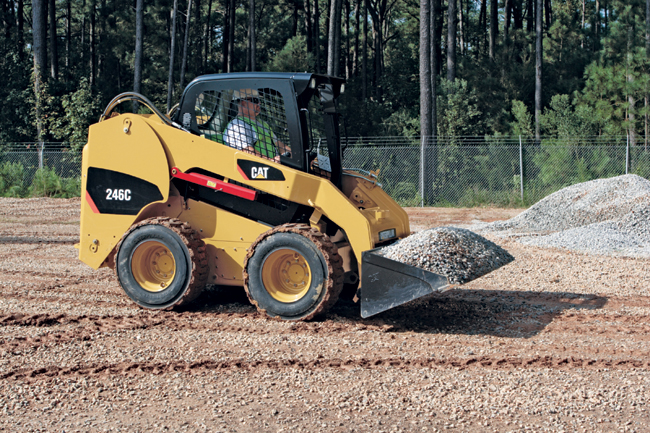
“It really boils down to the person,” says Scott Sloan, product engineering manager for Titan Tire Corp. “If that skid steer is vital to a person’s paycheck, then tire selection is extremely important because lost productivity will hinder the performance of the machine. Worn tires or tires improperly matched to the application will make the machine less efficient and ultimately cost money. On the other hand, if you only use that skid steer a couple hours a month, tire selection and overall condition of the tires may not be a concern.”
Tire wear is not an exact science. Many factors can lead to excessive tire wear, including the overall quality of the tire, application, routine maintenance and operator influences.
“As we visit with skid steer manufacturers, some expect the tire to last for 1,200 hours, while another manufacturer may only expect 400 hours of tire life,” says Sloan. “That’s a significant difference, assuming the contractor will put a total of 1,200 hours per year on a machine. If you’re only getting 400 hours of life from the tires, you can expect to go through three sets of tires each year. That can add up over the life of the skid steer.”
Pay Me Now or Pay Me Later
If you buy an inexpensive tire that has less tread depth and sidewall gauge, the potential for excessive wear is greater. However, you could spend 20 to 30 percent more for a better constructed tire that may provide up to 1,000 hours of tire life. It is a big decision to make, but contractors need to understand the cost associated with less expensive tires.
“There are price-sensitive shoppers out there, but if they take the time to run the numbers, they may discover paying that extra 30 percent will actually save them money down the road,” says Sloan. “Over the life of that machine, unless they need an overhaul, tires are going to be the most costly annual wear expenditure. It’s substantial.”
Wear — It’s Not Rocket Science
One of the leading wear factors is using the incorrect tire in the wrong application. A lug tire in an asphalt or concrete application will tend to wear faster than a tire designed for that application. Most skid steers are sold with the same tread design and end up being used in a variety of applications. However, depending on the application, the tire could experience more wear than a tire specifically designed for the application in which the machine will be used.
Another factor leading to excessive wear is the operator, as they have more influence on the wear and condition of the tires than anything else. Constantly spinning the tires when going into a load or making sharp turns has an effect on tire longevity. An operator with a softer touch, who makes wider turns and doesn’t spin the tires, can certainly help extend the life of the tires.
Inspecting Isn’t Like Splitting the Atom
“I wish I could say it’s real complicated, but it’s not,” says Sloan. “With a lug design on an R4 tread, the shallower the tread gets, the less traction you have and that affects efficiency. As the tire begins to wear, the operator will start noticing the shallowness of the center of the tire, and if it gets to the point where the center of the tire is smooth and the tire still has lugs on the outside of the shoulder of the tire — that’s an obvious sign that the tires are worn.”
Another way to notice wear is the feel of the machine. If the skid steer is losing bite when going into a load, the operator will notice the machine will not penetrate the load with the same power as if the tires were new. It’s all a compromise — how long can you accept less efficient performance before pulling the trigger for a new set of tires?
Sloan also encourages contractors to inspect their tires for inflation and debris.
“Inflation pressure is, by far, the biggest maintenance step a person can take to extend the life of their tires,” says Sloan. “If the tire pressure is too low, especially on a skid steer tire, an operator can actually walk the tire right off the rim and cause potential damage to the tire.”
Air pressure in the tire is what carries the load. If the tire pressure is lower than what is recommended by the tire manufacturers, then you’re making that tire flex more than it should and putting undue stress on the tire. This will affect how quickly the tire actually wears. Debris in your tires can also affect wear. A wood chip or a piece of steel that’s lodged in the tread design can eventually work its way into the tire and make the tire go flat. So it’s important to remove loose debris from the tires on a daily basis.
Selecting New Tires
When searching for a new set of tires, there are many factors to consider. First and foremost, what is the primary application? Will you be working in a concrete, dirt or landscape application? Your independent tire dealer needs to understand your business and how you’re going to use the tire. This information will help them recommend the appropriate tread design and the options within that style of tire.
Even piano man Billy Joel knew there’s no way of avoiding pressure. Note: Only the middle of over-inflated tires touch the ground, which makes the center of the tread wear faster. Conversely, the outer edges wear faster on under-inflated tires. |
If a contractor plans to spend 50 percent of his or her time working in asphalt and concrete and 30 percent in dirt, then he or she may want to lean toward a rock or concrete/asphalt tread since that will be the primary application. However, if the contractor plans to use the skid steer in dirt all the time, then he or she should look at an industrial R4 tread design. Landscapers working in established lawns may want to explore a R3 tread design to minimize turf damage and the machine’s footprint.
“It’s a world of compromises,” says Sloan. “Unless you work in a specific application, each contractor will need to make some sacrifices. On the other hand, we also have worked with contractors who stock multiple tread designs [rock and dirt] and swap out tires based on the application. They prefer the performance and would rather take the time to change out the tires to match that specific application.”
While a tire with a rock tread will wear exceptionally well in a rock, concrete or asphalt application, the solid lug design or high lug-to-void ratio, means there’s not a lot of gaps between lugs. Should the contractor get into muddy ground conditions, the tire will not get clean and just becomes slick with lack of traction. In those cases it’s best to switch tires and go with an industrial and dirt tread design.
Selecting the right tread pattern doesn’t apply only to replacement tires. If you purchase a new skid steer, make sure the tires are matched to your application.
Once you’ve selected the appropriate tread design, make sure the tires are properly sized to the machine. Each size skid steer requires a different tire rating and it’s important not to put a 10-ply tire on a skid steer where the manufacturer recommends a 12-ply tire. The manufacturer installed 12-ply tires on the machine for a reason. Substituting lighter ply tire may save money at the time of purchase but the tire will have less load capacity and less inflation pressure for the application. This can lead to excessive stress beyond its design in the application at hand. In other words, it will wear out faster and be more likely to fail on the job.
Most tires look the same from a distance, so it’s important to ask questions and visually compare competitive tires. Look at the inside of the tire. Take notice of the number of plies and the deck gauge. The deck gauge is the amount of rubber between the bottom of the lug and up into the tire casing. This provides puncture resistance and overall tire durability.
Sidewall gauge is another consideration. Skid steers typically experience a wide variety of ground conditions and take abuse from many different angles. The sidewall gauge is the thickness from the outside of the tire on the sidewall to the cords themselves. Most tires feature a trash guard or dirt shield that actually goes over the rim to keep dirt and debris from forcing its way in between the rim flange and the tire.
Skid or tread depth may look the same from a distance, but if you actually start measuring up skid depths, you will find that some are significantly less than others. In the skid steer world, skid depth equates to tread life. If one tire has a 20 percent deeper tread depth, one could expect 20 percent more life out of the tire. Now that tire is going to be more expensive, but the operator needs to weigh the pros and the cons.
In a demolition application contractors should select a solid core or non-pneumatic tire, especially if they will be driving over rebar and operating in extreme situations that may cause tire puncture issues. While these tires provide sheer durability, studies have shown that these tires can have a negative effect on the skid steer drive and power train over time.
Greg Ehm is a feature writer for Two Rivers Marketing, based in Des Moines, Iowa.
Comments are closed here.