Emission Control
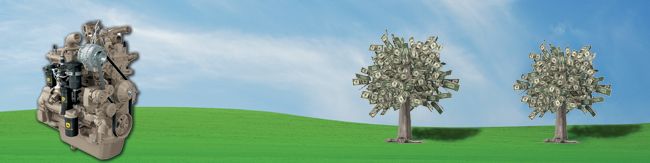
The most stringent yet of the EPA’s regulations for non-road diesel engines, known as Tier 4 Interim, effectively began New Years Day 2012 (at least for diesel engines in the 75- to 174-hp bandwidth). Since the Clean Air Act of 1990, both gas and diesel engine manufacturers for construction equipment have been intermittently designing new engines with high technologies aimed at significantly reducing the amount of pollutants released into the atmosphere by diesel power plants (these government-imposed regulations are called Tiers). The final and most intensive of these EPA Tier regulations — which is broken into two deadlines called Tier 4 Interim and Tier 4 Final — have diesel designers from Cummins to Caterpillar creating smarter, more complex and cleaner burning engines.
Of course all of this comes with a big price tag for the professional contractor, the engine maker and the manufacturer and distributor of construction equipment. New fancy-sounding technologies like cooled exhaust gas recirculation (EGR) and selective catalytic reduction (SCR) are being installed on diesel-powered equipment like excavators and wheel loaders to clean polluted exhaust. These new engine systems require more space, more maintenance and often generate more heat or require a new fluid (generically called urea). If there’s a Tier 4 Interim engine installed on the new piece of equipment you plan to purchase, it’s definitely going to cost more. But that price must be balanced with the idea that these engines nearly eliminate the dispersal of harmful byproducts like soot (nitrogen oxides or NOx) and particulate matter (PM).
“The emissions regulations can certainly seem daunting,” says Paul Holst, product manager for John Deere Power Systems. “But I think a lot of folks realize there is a need to clean up air pollutants, and the new technologies engine manufacturers are implementing definitely do that.”
A news release from the EPA from May 11, 2004, says that these regulations “will cut emission levels from construction, agricultural and industrial diesel-powered equipment by more than 90 percent. The new rule will also remove 99 percent of the sulfur in diesel fuel by 2010, resulting in dramatic reductions in soot from all diesel engines.”
By 2014 and Tier 4 Final, engines of all sizes will be required to meet NOx and PM reductions in their systems, pending a few massive-sized engine outliers. This, from the same EPA news release, will effectively cut “pollution equivalent to having some two million fewer trucks on the road.” The projected environmental benefits really are quite extensive.
The construction industry has adapted to previous Tiers 1 through 3 with mostly “in-the-envelope” solutions (things like common rail fuel systems and turbochargers). But some of these new Tier 4 technologies involved with EGR and SCR (or a combination of the two) require engineering issues to be more innovative. With Tier 4 Interim comes the advent of outside-the-engine components that are capable of reducing PM and NOx emissions to .01 g/hp-hr and 0.3 g/hp-hr, respectively. Diesel oxidation catalysts (DOCs) and diesel particulate filters (DPFs) clean the polluted engine air, but they also take up big space in the engine compartment.
Cooled EGR is essentially the opposite of SCR. Cooled EGR cools and mixes measured amounts of exhaust gas with incoming fresh air to lower the engine’s peak combustion temperature, thereby reducing NOx to an acceptable level. Because of the lower combustion temperatures used to reduce NOx with the cooled EGR approach, there is an increase in PM. To reduce PM to acceptable levels, exhaust gases are routed through an exhaust filter, located downstream of the engine, containing a DOC and DPF. PM is trapped in the filter and — through a process called regeneration which utilizes normal engine exhaust temperatures — is oxidized (burned) into nitrogen gas and carbon dioxide, then expelled through the exhaust pipe.
With the SCR approach, the technology increases the peak combustion temperature in the engine and the result is less particulate matter but NOx levels are increased. If mandated PM levels cannot be achieved, any further reduction in PM is accomplished by a chemical reaction in a DOC. To reduce the higher levels of NOx, a diesel exhaust fluid (DEF — also called urea) is injected into the exhaust stream downstream of the engine. When the exhaust gases combine with the DEF in the SCR catalyst, NOx is broken down into nitrogen gas and water vapor and expelled through the exhaust pipe. SCR technologies require contractors to occasionally add urea, which can be expensive and difficult to find in some cases.
The challenge for a company like Wacker Neuson is designing machines around Tier 4 engines to host new components like a DOC or DPF and to allow the engine to cool properly, says Marc Leupi, Wacker Neuson Americas’ utility product manager.
“We spend a lot of time on a full-blown development project, but it’s for a product we’re already selling, so we don’t get any revenue out of it,” Leupi says. “It’s just a lot more development cost without any new revenue for it.”
That cost Leupi talks about is inevitable across the board: Manufacturers have seen their development costs rise in developing ways to meet the Tier 4 Interim standards, which in turn is passed on to the end-user. Until now, the changes and subsequent cost increases have remained fairly minimal. “I hope that people will say, ‘OK, it’s part of life’ and move on,” says Dave Goodsell, sales manager of the Bobcat dealership in Omaha, Neb. “There were still price increases, but they weren’t as heavy as this.”
Bobcat announced an initial 5.25 percent price increase on Tier 4 engines that began Dec. 1, 2011. We’ve heard a lot higher from other machine makers. “All manufacturers will see price increases as a result of Tier 4,” says Chris Knipfer, marketing manager for Bobcat Co.
“Quotes we’ve gotten are direct double in price,” Leupi says. “It varies, but it can be anywhere from 100 percent or more — just for the raw engine.”
These prices will definitely hit contractors, machine makers and distributors hard. According to Mark Scoccolo, manager at SCI Infrastructure (a Seattle-based utility construction company), any increase in prices right now is a big burden for professional contractors.
“You talk to any contractor and any new equipment is too expensive across the board,” he says. Similarly to the manufacturers, contractors will have to factor the extra equipment dollars into the cost of construction, which ultimately rises, Scoccolo adds.
Though many Tier 4 Interim-compliant products are still rolling out, the eventual cost of these engines is inevitable. Exploring the used market is an alternative route to buying expensive new equipment, but there are only so many low-hour machines that have a high resale value. However, the EPA’s technical relief amendment for non-road diesel engines allows companies to keep making a small percentage of the previous Tier 3 engines while phasing in the Tier 4 Interim engines.
With new equipment comes the challenge of figuring out how to manipulate it effectively. Though the new engines are more complex, manufacturers have made extensive efforts to train dealers, issue pamphlets with frequently asked questions for the equipment operators and make the transition as easy as possible.
Concerns have arisen regarding the quality of the new environmentally friendly equipment, but manufacturers have made sure to reassure their clients that these machines are more efficient than ever. Scoccolo agrees.
“Overall, as far as the efficiency and productivity, it keeps getting better,” he says. “It’s good equipment. The manufacturers have certainly done a great job of making high-quality equipment for North America.”
Leanne Butkovic is a contributing editor to Compact Equipment, based in Peninsula, Ohio.