Building a More Efficient Office
Construction companies are great at what they do: building things efficiently, on time and on budget. Sometimes this philosophy gets lost when it comes to the day-to-day operations that are essential to running the back office. Keeping up with change orders, material delivery, invoice approval and all the other project-related items can become very time consuming. Fortunately, Electronic Document Management Systems (EDMS) can quickly eliminate the pain points that go along with the vast amount of paper associated with the construction process.
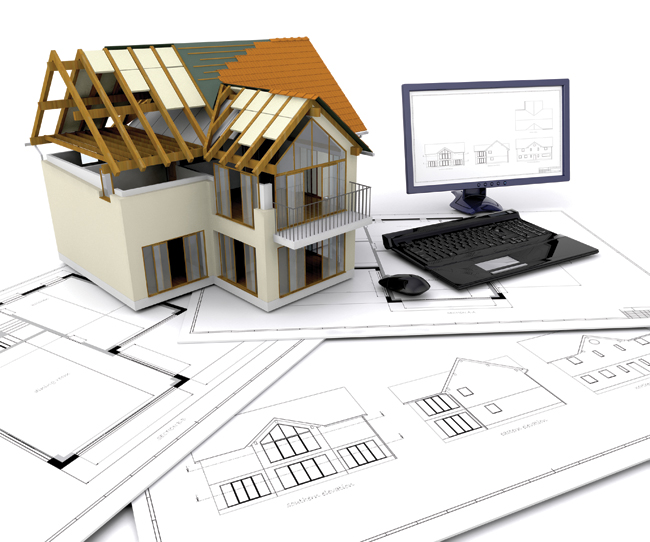
Implementing Document Workflow Processes
Every business has some sort of document workflow process in use. Whether that process is limited to a single individual or multiple people, documents usually flow through a series of steps as part of the daily business process. Document workflows may include invoices, orders, e-mail, snail mail or any other document processed every single day in every single business. Once the realization of how often document workflow occurs each day, one begins to consider ways to improve and streamline the document workflow process to maximize time and cost savings.
Where to Begin
Workflow is the step-by-step procedure taken to complete a job. Construction businesses need to consider the possibilities of automated workflow using document management when real problems occur. This usually manifests as some point of “pain” in the physical process of dealing with paper. Some points of contention when dealing with paper may include:
- Loss of documentation
- Unable to quickly locate information for customer service responses
- Meeting compliance requirements for audit or security
- Rising costs of additional staff to process paper based workflows
- Efficiency in managing the paper based workflow for tracking and status purposes
- Movement of paper between a remote office and a corporate office
Once the decision is made to improve workflow, the question becomes, “Where do I begin?” The first thing to do is choose one document process to work with. Oftentimes, the biggest mistake a company makes is trying to improve all processes at one time. This seldom works and many times ends up as a failed attempt to automate any process. Some examples of construction processes that can become extremely efficient using EDMS are the delivery of documentation from the construction site to the main office and approval of project management documents such as invoices and change orders.
After selecting the process to improve, the process can be broken down into actual physical steps. Take the business process and physically follow it from beginning to end. Spend time with each person involved along the way and find out what action items occur at each step, what the exceptions for each decision are and where the document goes once it leaves that step. The end result of this will be a clear understanding of what takes place for the entire process under review.
As the review is taking place, imagine the process residing in an electronic workflow. Think about how the physical process will work electronically or if it will even work electronically. For example, one step of the process may involve an outside entity applying a signature to the piece of paper. How will this work if the document is electronic? Make note of any potential pitfalls of applying electronic technology to the workflow process. Build a list of process requirements and use it when selecting a vendor/product for implementation.
Choosing the Best Technology
With the workflow process understood and requirements gathered, it’s time for product selection. Start by making a product feature list and specifying whether the feature listed is required or optional. Share this list with various vendors so they can respond to your needs. Base the list on the information gathered as the workflow process is analyzed and the workers interviewed. Ensure that the selection guidelines include gathering of the following information from the vendors as you request information:
- What are the system hardware requirements? This ensures that the correct computing infrastructure is in place to run the software efficiently. Without proper hardware, the software may not run at optimum performance, thereby negating any time savings anticipated from implementation of an electronic process.
- What are the requirements for any specialty hardware such as signature pads, scanners or web servers?
- What is the cost for software maintenance and technical support?
- What is the availability of technical support?
- What are the reference accounts for similar size companies?
- How is the data backed up?
- What training programs are offered?
- What is the availability of professional services for integration and custom processes?
- Is the software proprietary or is it built on an open architecture?
- Can the system be installed on premises or hosted in an SaaS environment?
- Is a software development kit or application programming interface (API) available to allow for integration to existing software products?
Vendor or product selection should not be based solely on cost. The product should meet the critical functional requirements and have the flexibility to grow with your business. Ease of use and speed of deployment are also key factors to look for when selecting a product. Avoid products that require excessive customization and programming services to make the basic functions of the workflow process work. This step alone can cause major delays and cost overruns. The majority of items on your requirements list should be available “out of the box.” Customer service and support are also extremely important elements of the total solution. The product selected may perform well but without service and support, undo frustration may arise when the need for help is warranted.
Quantifying the Results
There are many benefits of automating your document workflow processes. One example is the “missing document.” This is a frequent issue with paper-based, and even with electronic documents, that are not stored in a controlled repository. A document is handed to or e-mailed as an attachment to a person for review and approval. That e-mail or document is subsequently lost or accidentally deleted. There are many problems that can arise. Who will know that the document is missing? Will the person who sent it know to follow up and request the approval? If so, will that person be able to re-create the lost document? And what if this document was a customer order or an important equipment requisition? Studies show the average cost to re-create a lost document is $250. These “missing document” episodes happen every day in most businesses and they inherently take a tremendous toll on a business, both financially and in damaged customer service and competitiveness.
Conclusion
Is your construction business using outdated and inefficient workflow methods given today’s availability of affordable and easy-to-use software technology? Taking your business to the next level is easier than you may think. Pick a single workflow process, analyze this process at each step and create a diagram to document the process. This approach will put you on a solid path toward continuous improvement of your business workflows that make your organization more efficient, competitive and profitable.
Abe Niedzwiecki is vice president of technology for document management software and workflow provider Cabinet NG, based in Madison, Ala.