Avoiding Pump Problems
Hydraulic submersible pumps are designed for dewatering jobs in tough locations — construction, mining and sewer rehab projects. The benefit of using a hydraulic submersible pump is that it can be used in areas that would flood and disable a conventional pump. They’re well suited for open pits, lake un-watering, manholes, flood control, mining and sewer bypass pumping. The pump head requires less space requirements at the point of pumping, so a well designed 6-in. hydraulic submersible will fit into most manhole openings. Hydraulic submersible pumps are made to work in some harsh underwater conditions, which means they will need a little extra TLC when it comes to regular maintenance in order to keep working project after project. While pumping systems can seem like fairly complicated pieces of equipment, most contractors with a toolbox and a little experience can tackle some of the maintenance basics.
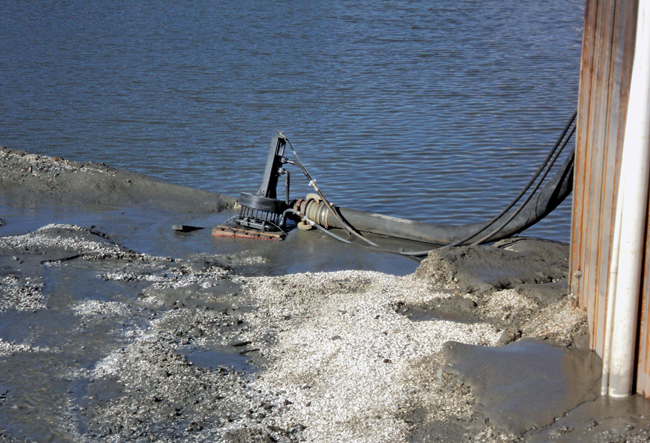
So, Just How Complicated Is It?
In reality, a hydraulic system is not a complicated system. As with any pump system, there are some basic components involved — a driver, the impeller/pump and the transmission. The basic difference is that instead of a flexible coupling or gear train, the transmission is a hydraulic system. The hydraulic system is composed of a hydraulic pump, hydraulic motor, supply tank, filtration method, cooling method and transfer lines. The driver puts power to the pump and moves fluid from the reservoir. It converts the energy from mechanical to fluid pressure and volume through the lines to the motor and transfers the energy to the shaft and impeller to move the pumped liquid. The fluid is then routed back to the supply tank through a cooling system and filtration system to repeat the process. So, although there are a few more components than a simple coupling system, hydraulic submersible pumps convert energy through pumped fluid like other pumping units.
What Is Really Required to Operate and Maintain the System?
The most basic of maintenance checks that will be required is to check for leaks and general wear part, and to maintain fluid levels. These are items that can and should be done every day. A large number of maintenance failures are the result of easily fixed problems. Also, it is important to watch the temperature of the fluid because heat can decrease the efficiency of the system and damage components. Filters should be inspected and changed on a regular basis. Engine and drive manufacturers provide guidance on recommended service intervals that should be followed and adjusted based on actual operating conditions. On the hydraulic system, the filters will help to keep the lines flushed and there will be some wear over time. But with proper filter maintenance, the system will be quite effective.
Select the proper fluid. All oil has certain limits whether it is for the hydraulic system or the engine. It is important to look at the pumping application and the environment to determine what works best. In cooler temperatures, an AW32 may be better. In warmer climates, an AW68 could be considered. Especially if the fluid is in an area where it could affect the environment, a biodegradable may be preferred. However, it should be maintained so that condensation or contamination does not cause the oil to start to break down.
Other maintenance factors are similar to any pump or engine. One is to protect against damage caused by abrasive materials. It is important to check the compatibility of the materials of construction and the materials being pumped to make sure that they fit. Wear rings and wear plates should be adjusted periodically to keep the efficiency of the pump where it should be. Impellers should be inspected for damages. Look at the ability of the materials you use to be easily repaired if abrasives are a factor. A fabricated component is sometimes easier to weld and repair than a casting that will require special welding materials or techniques. Another frequently addressed area for maintenance is seals and bearings. They should be properly lubricated. Watch them for signs of heat and overloading. A bearing problem can amplify and result in additional problems with other parts of the system.
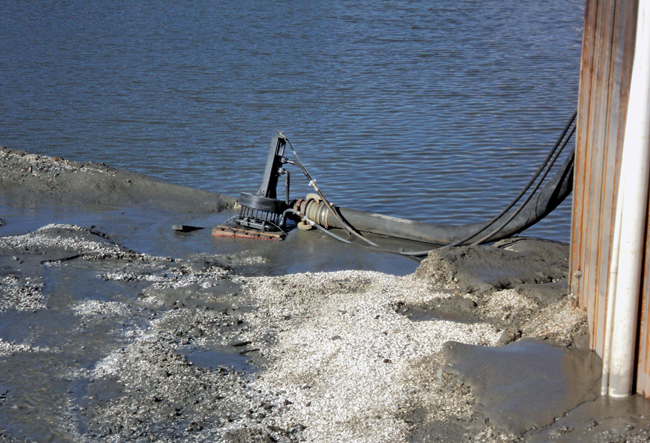
And lastly, one of the unspoken maintenance items is to watch for signs of abuse, misuse or mishandling. As pumps are moved around a site, they can bounce and get bumped. Sometimes an unfamiliar operator or mechanic can create more problems than they fix.
Should I Consider an Alternate Model?
So, when you go into the dealer and he suggests that new model of hydraulic submersible pump, what are the advantages? On a hydraulic pumping system, some factors are:
- Suction lift restrictions are eliminated.
- You have the ability to remote mount the power unit to protect against flooding, jobsite damages or provide more space for site operations.
- There’s improved efficiency.
- There are more environmentally-friendly options.
- It’s easy to maintain and repair the pump head.
- You can work on the pump head without having to deal with the power unit.
- There are a variety of pumps available to be driven with the same power unit.
Overall, a hydraulic-driven submersible pump does not have a significant amount of different items to maintain than a standard pump and may provide more options with the same piece of equipment. Of course when selecting the right pump, don’t go to the nearest salesperson and tell him you need a hydraulic-driven submersible pump. Tell him or her what you need the pump to accomplish. A salesperson may give you what he or she has in stock or on the shelf, but a pump and dewatering professional will evaluate your application and give you the right tool.
Tom Aldridge is a sales engineer for Griffin Dewatering, based in Houston.