Alternative Fuels Propane
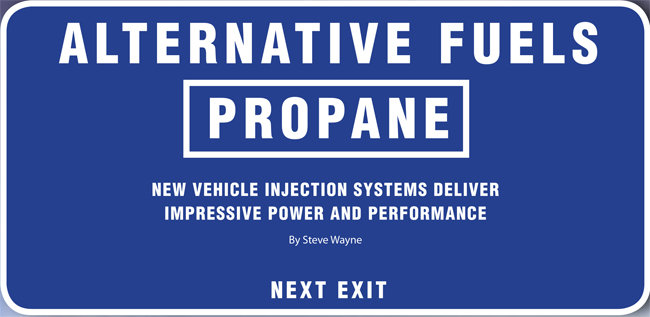
Alternatively fueled commercial vehicles have been around for a long time. Did you know the first vehicles fueled by propane autogas were originally developed in 1913? Back then, vehicles commonly used what’s called a vapor pressure system, similar to an older carburetor system, powering cars with an innovative propane-fueled engine. Nearly 100 years later, these technologies are becoming viable options again to help fleet managers.
Since vaporized propane autogas systems were often associated with a loss of power, manufacturers have been inventing new ways to meet the performance, economic and environmental goals of professional contractors and truck drivers today. Specifically, the Propane Education & Research Council (PERC) has been collaborating with several leading manufacturers and well-known automakers for years, looking for a solution. PERC provided funding for research and development of dedicated liquid propane autogas injection systems, which deliver equivalent performance and reduced emissions compared with conventional gasoline fuel systems on trucks.
In the past two years, more than a dozen new vehicle platforms fueled by propane autogas have been developed. Light- and medium-duty truck, shuttle and van applications are available from Roush CleanTech through a partnership with Ford Motor Co., and CleanFuel USA through a partnership with General Motors. Additional vehicle platforms are in development, and here’s an update on those evolving technologies.
Dedicated Liquid Propane Autogas Injection Systems
As an engine fuel, propane autogas has a high-octane value and beneficial chemical properties for spark-ignited internal combustion engines. In the older engine systems, propane autogas would vaporize and mix with combustion air in the intake manifold of the engine. This would lead to lower engine output, as the vaporized propane displaced air that is the critical ingredient for power in the engine.
Dedicated liquid propane autogas injection systems have multi-port liquid injection that delivers liquid propane autogas directly into each cylinder’s intake port. These systems provide the same horsepower, torque and towing capacity as gasoline-fueled versions of the same models. The systems completely replace the original manufacturer fuel systems, requiring removal of the manufacturer’s fuel tank assembly, fuel line assembly and fuel rail assembly. The new propane autogas system components are then installed.
Key Components of the System Include:
Fuel Rail Assembly: Dedicated liquid propane autogas V8 injection systems use two symmetrical billet aluminum rail halves. Each rail half is fitted with four propane-autogas-specific fuel injectors. One rail half is fitted with an injection pressure and temperature sensor, which are utilized by the engine management system.
Fuel Line Assembly: Dedicated liquid propane autogas injection systems feature a return fuel-line subsystem. As the fuel pump turns on and starts pumping fuel through the lines, the injection pressure and temperature sensor determine if the fuel is a gas or a liquid. If it is a gas, the fuel passes through the fuel lines and returns to the tank. When liquid starts to run through the sensor, a flow control solenoid opens and the ignition process begins.
Fuel Tank Assembly: The fuel tank assembly and vehicle installation location varies by vehicle model; all propane autogas tanks replace the originally manufactured fuel tanks. Propane autogas tanks are made of ductile steel and certified to ASME standards and are 20 times as puncture-resistant as typical conventional fuel tanks. As with conventionally fueled vehicles, to transfer the liquid propane autogas from the fuel tank to the engine, the fuel tank assembly contains a single fuel pump, controlled by the powertrain control module (PCM).
Powertrain Control System: Manufacturers like Roush CleanTech and CleanFuel USA are able to recalibrate the standard OEM powertrain control system for optimum performance on autogas. The use of the standard OEM service tools are retained to ensure the service experience is transparent operating on propane autogas.
High Performance with Reduced Emissions
Fleet managers are realizing there is little difference in operation or performance in vehicles fueled by propane autogas compared with gasoline-fueled equivalents. The modern liquid propane autogas fuel system and on-board PCM recalibration allows the vehicles to deliver equivalent performance, while emitting fewer greenhouse gas emissions.
On average, fleet vehicles fueled by propane autogas emit 12 percent less carbon dioxide, about 20 percent less nitrogen oxide and up to 60 percent less carbon monoxide than gasoline-fueled vehicles. The systems developed by Roush CleanTech and CleanFuel USA also meet government guidelines, including Environmental Protection Agency, California Air Resources Board, National Highway Traffic Safety Administration, Federal Motor Vehicle Safety Standard and National Fire Protection Association.
Fleet managers interested in vehicles fueled by propane autogas should contact their fleet dealers or vehicle manufacturers. For more information about PERC and vehicles fueled by propane autogas, fleet managers may visit autogasusa.org or contact their local propane autogas providers.
Steve Wayne is the chief commercial officer of the Propane Education & Research Council, based in Washington, D.C.
Tier 4 Diesel Engine Testing
Sophisticated New Test Facilities Help Perkins Engines Survive in a Rough World
“Our lives would be much easier if the world was flat and level, but it isn’t and we have to deal with the consequences of that fact,” explained Mike Looney. As operations manager of Perkins Engines Co. Ltd.’s Global Engine Development center (GED) in Peterborough, England, Looney’s responsibilities include determining just how the company’s products react to the ups and downs of real-world operation.
The company has invested $31 million in GED over the last three years, including 12 new validation cells and upgrades to five existing cells. Along with this expanded ability to test and validate its new Tier 4 engines, Perkins has also added a tilt cell that allows workers to check performance while simulating the typical and extreme altitudes an engine would see in customer applications.
“A conventional test cell can tell you many things about an engine,” Looney said, “but it won’t give you any information about how it responds to being tipped up and down, or rolled from side to side or even turned upside down while it’s running. All of those things happen in the real world, and we need to know how our engines react.”
Perkins’ tilt cell has a hydraulically-actuated table that can rotate a fully-instrumented engine through 180 degrees on the crankshaft axis, and it can tilt up or down 45 degrees off horizontal while it’s running. A typical test includes a battery of tilts and rotations that mirror actual conditions the engine is likely to meet in use. What the engineers are most commonly looking for is a loss of oil pressure as the pump loses suction. To monitor this, they equip the test engines with sensors that read the oil pressure from the “full” and “add” marks on the dipstick gauge while tilting and rotating the engine at various fixed and dynamic throttle settings.
Perkins’ GED has approximately 50 standard test cells and several specialized cells like the tilt unit to support a variety of complex validation tests, including performance and emissions, mechanical development, endurance and transient development.